Although marking and coding formats provide product-specific information, such as information about a product’s price, manufacturing date, batch number, expiry date and shelf life, experts note that new technologies are further assisting beverage operations by improving supply chain traceability and product visibility.
“We are seeing two central themes impacting the beverage industry as it relates to coding and traceability equipment,” explains Ryan Petty, strategic account manager at Chicago-based Domino Amjet.
The first theme involves the evolution of connectivity and utilization of real-time data, Petty says.
“Manufacturers, particularly in the beverage industry, have a need to be flexible, agile, and offer an efficient production environment. A part of this requires turning real-time data into actionable insights for better decision-making,” Petty explains. “This also entails connecting assets and technologies. Automation can help reduce the time needed for line changeovers overall, and it can help reduce the potential for errors when entering new coding data.
“Even without integration into a larger manufacturing system, connected coding and marking equipment can alert operators when any parameters are approaching an out-of-spec condition or let them know ahead of time when consumables are running low or maintenance will be required,” he continues.
The second theme revolves around sustainability, specifically reducing waste, including waste caused by human error, Petty notes.
“Now consider that the average human makes one mistake for every 300 characters entered, it results in substantial opportunities for errors to arise,” he says.
Yogi Vasudeva Nayak, vertical marketing manager at Videojet Technologies, Wood Dale, Ill., notes that, with the growing trend toward canning, especially in craft breweries, advanced coding and marking technologies can offer beverage operations more efficient solutions.
“As more brewers choose cans over bottles to promote freshness and reduce transportation costs, new advances in fiber laser marking technologies are offering more efficient means of applying lot and date codes on cans,” he explains. “At the same time, continuous inkjet (CIJ) printers are available to deliver excellent print quality at ultra-fast canning speeds.
“Whatever the chosen coding solution, it must run with minimal interruption in the harsh environments of high-speed beverage operations,” he continues.
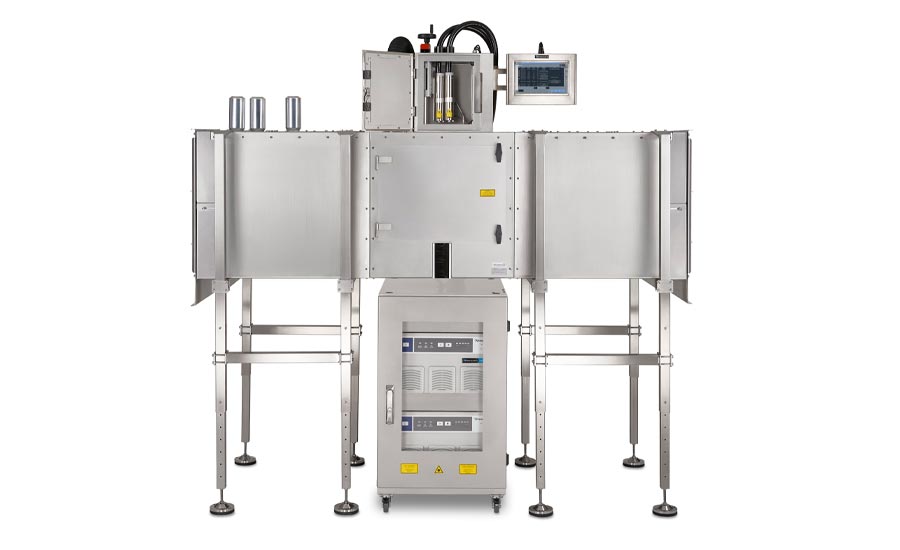
Image courtesy of Videojet
Optimal uptime, interconnectivity
As the days of selling technology as one-offs are gone, Domino’s Petty notes equipment manufacturers need to take a consultative approach when working with beverage manufacturers, which begins with understanding their objectives.
“Additionally, equipment will need to offer the industry 4.0 capabilities,” he says. “Artificial intelligence, digital twins and augmented reality will optimize machine design, development, operations and maintenance within the next five to 10 years. Data will help optimize the manufacturing process as more data analysis experts enter the field.”
Further, as beverage-makers take it as a given that the technology they use is reliable and supported effectively to minimize downtime, Petty notes the new expectation is threefold:
- Expect the coding technology will reduce waste and support their sustainability goals
- Support faster throughput
- Support connectivity
“IIoT is the next major advancement in automation, enabling machinery and equipment to transmit real-time information to an application,” Petty adds. “Operators can use this information to better understand equipment efficiency, identify maintenance needs, and prevent failure and loss.
“More efficient date coders, such as those offered by Domino, also provide companies with automation expertise and insight on more efficient print practices,” he continues. “This allows manufacturers to achieve optimal uptime and true interconnectivity, and minimize operator errors.”
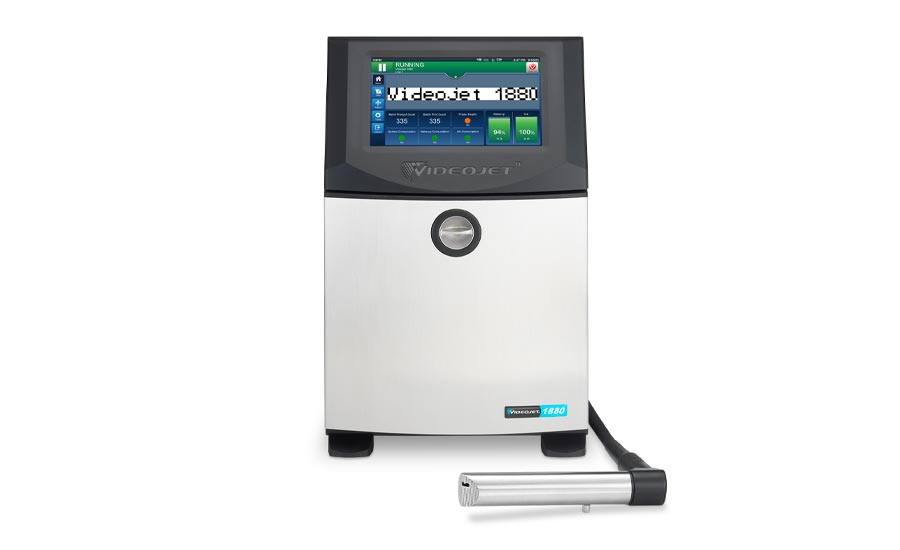
Image courtesy of Videojet
Coding technology’s ongoing evolution
Experts note that coding solutions designed specifically for the beverage industry are helping manufacturers overcome unique challenges.
“While support is a given from the perspective of the beverage processors buying the technology, the way things are supported has changed,” Domino’s Petty notes. “Onsite and remote support that is effective, quick and proactive has become a necessity.
“For example, [by] using the Domino SafeGuard Augmented Reality in a secure virtual service environment, customers can show Domino’s remote personnel exactly what is occurring on the line,” Petty continues. “The ability to ‘see’ with the customer’s eyes makes it quicker and easier for service staff to identify the cause of line issues and implement fixes.”
On the technology side, Petty adds that, “IIoT and efficient coders can help manufacturers create more efficient processes and collect and analyze information about these processes, leading to reduced waste and improved sustainability.”
Nayak notes that while VideoJet’s Lightfoot canning solution is a comprehensive system, it is backed by the ongoing application support of Videojet Connect Remote Service, which delivers the reliability and performance necessary to achieve beverage production goals.
Moreover, the Videojet Lightfoot canning solution “features dual fiber marking heads that provide built-in redundancy, keeping the line running in case of a fault,” Nayak says. “The solution is capable of ultra-fast speeds, is robustly designed for harsh environments and delivers high-quality, precise laser codes in a single all-inclusive system. It is engineered with a Class 1 sealed enclosure that blocks all laser emissions, preventing any possible injury from optical radiation during operation.”
Further, compared with continuous inkjet (CIJ) coders, Nayak notes that lasers offer a better overall print quality when marking text, barcodes and logos.
“Marks made with lasers are permanent,” he explains. “Unlike CIJ coders, laser marking systems do not use inks or solvents, so the purchasing and storing of consumables and the operating costs associated with keeping printers filled with consumables are eliminated. A range of marking fields helps lasers accommodate various product sizes and line speeds.”
Domino’s Petty echoes similar sentiments, noting the numerous benefits available when using laser coders.
“Throughputs have dramatically increased, connectivity is more advanced, and the contrast of codes has evolved,” Petty says. “Domino’s fiber laser coding technology offers a more environmentally friendly, waste-free, and efficient alternative.
“Fiber laser systems create high-regulation codes and logos, even on concave surfaces, and can code bare, uncoated and anodized aluminum,” he continues. “The ink-free coding process has the highest uptime on canning lines and the lowest impact on overall equipment effectiveness.”
Looking forward, Petty adds that, as the equipment on production and packaging lines continues to evolve, manufacturers are taking note of “interactive/intuitive human-machine interfaces (HMIs), smarter sensors and safety improvements as the next steps toward smarter machines.”
“Remote diagnostics, networking and overall connectivity, support of higher speeds and vision integration; these are all the directions that coding technology is going,” he concludes.