Best known for his pioneering work in programming languages in the 20th Century, computer scientist Adam Perlis said: “Simplicity does not precede complexity, but follows it.” Today, with eCommerce, SKU proliferation and labor shortages posing additional challenges to beverage operations, experts note that voice picking solutions can help simplify the complex challenges that warehouses now face.
There are two “huge” beverage market trends currently affecting warehouse operations, says Mariah Holcomb, product manager for warehouse management solutions (WMS) at Encompass Technologies, Fort Collins, Colo.
“The first trend is the labor shortage that is impacting all tiers of the supply chain,” Holcomb notes. “Warehouses are seeing a high turnover of the workforce, which means efficiencies can take a hit when there aren’t consistent workers who are familiar with the products, layout and technology. Warehouse maps, voice picking and other guided technology help retain employees and maximize workers’ efficiency because a worker needs to know a lot less to succeed right out of the gate.”
The second trend revolves around picking procedures, she explains.
“Though restaurants and bars are ordering more products again, the impact of the pandemic has forced warehouses to rethink the organization of their picking,” she says. “When selling to bars and restaurants with smaller orders, usually all of the route pallets are picked by product, meaning fewer stops in the warehouse during the picking process. When pandemic sales shifted to more deliveries to big box and chain stores, the amount of stops pickers made increased because those types of retailers usually get their own pallets. Rather than picking 10 cases of one product, they’re picking two cases of 20 different products for one customer’s pallet.
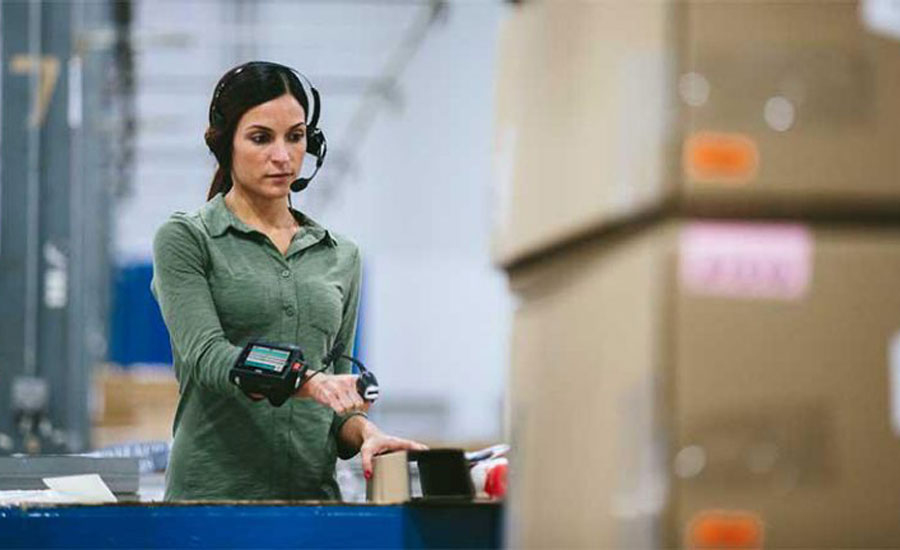
Image courtesy of Zebra Technologies
“This means warehouses need to be smart [about] how they slot their products and how voice picking technology efficiently guides their pickers to each of those picking stops,” she continues.
Kyle Nevenhoven, principal consultant for Atlanta-based Dematic, echoes similar sentiments noting that, with labor market trends continually affecting beverage operations, more warehouses are turning to automated solutions.
“The labor market continues to have a major impact on warehouse operations,” he says. “This is making distributors and warehouse operators consider different selling and picking time patterns, an increased focus on ergonomics, and a desire to pursue automation.”
Moreover, with retail markets revolving around service level agreements, warehousing and delivery operations face continued pressure by way of smaller and more frequent deliveries, he notes.
Voice picking solutions help address eCommerce issues
Where eCommerce is having a large and growing impact on distribution, experts agree that this typically results in beverage operations handling a higher number of small unit orders.
“At face value, eCommerce is making it easier for retailers to place orders whenever they want, and it’s increasing order amounts ― Encompass saw an 18.3% increase in average order volume when retailers used the DSDLink online ordering platform,” Holcomb notes.
Yet, the challenge warehouses face is that orders can come in at any time of day, which means a need for greater flexibility, she says. “It becomes a balancing act of picking based on a route and picking as soon as orders come through and are available to be picked,” she explains.
Mark Wheeler, director of supply chain solutions at Lincolnshire, Ill.-based Zebra Technologies, notes that, as eCommerce activity requires flexibility and speed, more warehouses are turning to newer warehouse solutions.
“These orders require high accuracy and a rapid turn-around time. As a result, the eCommerce segment will often require new warehouse workflows for efficiency and effectiveness,” he explains. “These workflows will have to be supported with new IT systems along with new approaches to edge technology such as wearable computers and voice-directed solutions.
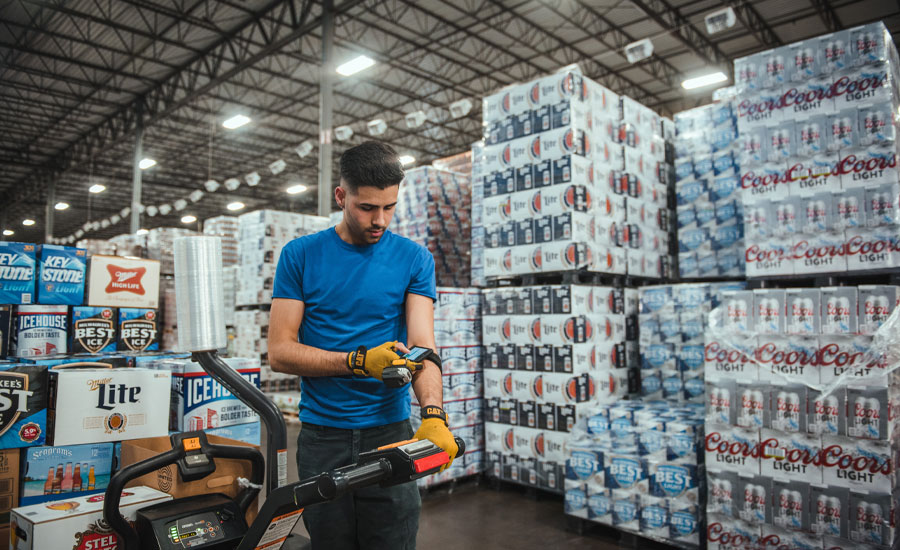
Image courtesy of Encompass Technologies
“They will also typically require new product storage schemes and sometimes physical automation including conveyors and mobile robotics,” Wheeler continues.
Still, eCommerce “thus far has not impacted the beverage warehouse industry to the same degree it has impacted other vertical markets (general merchandise, grocery, etc.),” Dematic’s Nevenhoven says.
“Distribution laws in most states and municipalities prevent beverage alcohol distributors from direct-to-customer sales,” he explains. “While this limits the exposure to the impacts of eCommerce, the retailers that the distributors serve are taking part in eCommerce, which may ultimately impact the service level expectations of these retailers.”
Nevertheless, eCommerce is an emerging trend in the non-alcohol beverage space, with the expectation of continued growth, Nevenhoven notes.
“Most beverage warehouses, outside of wine and spirits, are not prepared to sell in less than full case quantities, so process and layout alterations are required in order to economically participate in eCommerce activity,” he says.
The SKU proliferation effect
As SKU proliferation is only increasing as a trend, experts highlight the ways in which this trend is affecting beverage operations.
“The beverage industry is now starting to catch up to others ― including auto parts, grocery and apparel ― in SKU proliferation,” says Karen Bomber, senior director of marketing at Honeywell Productivity Solutions and Services, Charlotte, N.C.
The additional sets of SKUs now, drastically increases the beverage industry’s complexity, she notes.
“Before the increase, there was less focus on locator systems or cubing ― pallets were easier to build because many of the SKUs were identical in size,” Bomber explains. “With these additional SKUs ― from around 250 SKUs five to 10 years ago to nearly 1,200 SKUs today — it’s more in-line with other industries, although the SKU proliferation is still much smaller than others.
“The complexity of the warehouse operation goes up with more SKUs, and the beverage industry is going through what some might call the ‘clumsy teenage’ years of trying to figure out how to best deal with the complexity,” she continues. “As it grows, accuracy and efficiency are becoming more vital to increase profitability and limit errors. Having a flexible solution like voice picking technology can help to make the transition to larger SKU volume much more manageable.”
Zebra’s Wheeler echoes similar sentiments, noting that SKU proliferation adds complexity to the entire process.
“Adding SKUs may require changes to warehouse layout including going from bulk to racked storage,” he says. ”The pick line will require more facings. Some of these may require frequent replenishments and the labor required goes up as there are more location visits and pick lines per route and per pallet.”
Voice picking, integrated solutions enhance worker efficiency
Whereas robotics and some automation can take a long time to implement within a warehouse or distribution center (DC), experts note that voice picking solutions immediately can help the warehouse worker.
“It is not uncommon to have a [return on investment] (ROI) in less than a year,” Honeywell’s Bomber says. “Voice workers typically require very little training or onboarding because the system guides them through the process. Voice automation technology provides a simple and straightforward method to rapidly get workers up and running in the DC ― ensuring that the mobile worker is equipped to succeed from day one.
“As more automation is being implemented in a facility ― like cobots ― voice automation technology can become more seamless throughout the DC, helping to complement the mobile workforce,” she continues.
As voice picking solutions can integrate “rather easily” into enterprise resource planning (ERP) systems and modern WMS, pre-planning is crucial, Dematic’s Nevenhoven notes.
“It is critical that the operations team gives proper thought and consideration to the organization of the warehouse prior to launching a voice application such as the sequence of picking certain SKU packaging types, area congestion, etc.” he says. “This pre-planning work is crucial to obtaining quick adoption of the voice systems and realization of the quickest ROI.”
Encompass’ Holcomb notes that although voice picking technology can work on its own, it’s becoming more important for the technology to work in sync with other warehouse technology.
“Voice picking is effective on its own, but warehouses see the greatest benefit when they have smart warehouse map planning and technology that directs a pallet to be built in a way that ensures the safety of the product and people handling the pallet through the supply chain,” she says.
Zebras Wheeler echoes similar sentiments noting that today’s voice-picking solutions can be “architected with the WMS system driving the workflow” or with the voice solution optimizing the tasks on behalf of the WMS.
“In either case, the real-time data exchange between the voice system and the WMS is critical,” he says. “Exceptions have to be handled elegantly and intuitively for the worker.”
Improved technology brings advanced solutions
As voice picking technology has improved, experts note that the technology now is considered a primary solution for warehouses.
“Voice-picking technology has seen voice recognition greatly improve,” Encompass’ Holcomb says. “A few years ago, you would have to say something a couple of times because the warehouse was too noisy or the recognition technology wasn’t quite there. If you said ‘five,’ it might have heard ‘arrive.’ For the most part, pickers only need to say a command once with the current voice-picking technology.
“We’re also seeing voice-picking technology be complemented by hands-free scanning,” she continues. “With scanners that fit on a single finger or the back of the hand, pickers can verify in real-time that they’re grabbing the right case, while still using voice commands to move forward in the picking process.”
Zebras’ Wheeler notes that standardized hardware, mobile devices, and accessories like wireless headsets are widely available and now deployed in chilled and ambient facilities.
“Software solution provider offerings have also matured and can readily enable most workflows,” Wheeler says.
Additionally, voice applications now can run on less expensive, consumer grade electronics, reducing the equipment investment required, Dematic’s Nevenhoven notes.
“Some providers have added a visual component to the voice picking process, allowing the operator to see or respond to commands both by voice and by touchscreen interaction,” he says. “Some view this as a positive, in that you can see your next task or acknowledge the completion of a task without waiting for the voice command prompts to complete.”
As voice picking systems are being paired with some levels of automation, Honeywell’s Bomber notes that the environment can become safer and more efficient for both the worker and others in the warehouse.
“All the quality key metrics ― productivity improvement, quality improvements (selecting the right items/quantity), reduced probation time, employee turnover and safety are all helped by using voice picking technology,” she says. “As a result, voice automation technology is considered a primary solution.”