When asked what Apple is all about, the late Steve Jobs said, “Apple is about people who think ‘outside the box,’ people who want to use computers to help them change the world, to help them create things that make a difference, and not just to get a job done.”
Similarly, within beverage operations, where increasing SKUs, staffing issues and beverage trends pose challenges for warehouses, experts note that voice-picking technologies not only help get a job done, but work to streamline beverage operations as a whole.
“Transitioning from a few to many SKUs, like in beverages, requires adaptable solutions like voice-picking technology to maintain accuracy,” says Taylor Smith, chief marketing officer at Charlotte, N.C.-based Honeywell Productivity Solutions. “In today’s supply chain, perfection is essential to avoid negative customer experiences and costs.
“The industry is different in that there is an immediate need — if your beverage is not on the store shelf, you’ve completely lost the sale,” he continues. “Your consumer typically doesn’t come back the next day to see if it’s available.”
Kyle Nevenhoven, principal consultant of food and beverage at Atlanta-based Dematic, points to SKU proliferation as affecting nearly all operations within the warehouse.
“From a storage perspective, SKU proliferation has changed pallet storage requirements from those that are designed for large quantities of the same SKU and same date code to storage types that require high selectivity,” he explains. “The need to allow for a greater number of pick locations within the picking area also creates a different profile of pick location types, from all pallets to a combination of pallet, half pallet, and carton flow.
“The labor required to replenish half pallet quantities and carton flow is significantly greater than what is needed to replenish full pallets,” Nevenhoven continues. “Lastly, and most significantly, SKU proliferation has reduced picking productivity, creating more travel to pick the same number of cases and picking fewer cases from each location.”
Peg Ray, principal managing consultant at Encompass Technologies, Fort Collins, Colo., echoes similar sentiments, noting that today’s warehouses are challenged with having to efficiently and effectively store an increasing number of package sizes and configurations.
“Space management becomes the focus of daily operations; finding the shortest distance to travel to pick the higher volume products while at the same time, being able to locate the slower moving, but critical to the portfolio lower volume products,” she explains. “Picker management tools are imperative for an efficient warehouse operation.”
Addressing labor issues
As staffing challenges persist within beverage operations, experts highlight how voice-picking systems not only enhance warehouse operations, but help create better work experiences, leading to employee retention.
“Staffing challenges in warehouses were exacerbated by the pandemic and persist today,” Honeywell’s Smith explains. “While there’s been slight improvement since the pandemic’s onset, it remains tough to find and keep employees. Typically, these warehouses and distribution centers (DCs) are in proximity of each other — and they are vying for the same workers.
“While wages are key in holding on to employees, providing technology like voice systems and enhancing worker experiences also improves retention,” Smith continues. “Some companies incentivize productivity with tools like voice, allowing for higher wages despite similar pay rates.”
Dematic’s Nevenhoven points to staffing challenges that have created a need for beverage distributors to re-evaluate many parts of their operations, including order cycles, shift patterns, and delivery methods.
“Traditionally, much of the picking operation occurs overnight,” he explains. “As it has become increasingly difficult to attract and retain staffing on night shift, distributors are looking for ways to move much of the picking operation to occur during the day. In some cases, this is accomplished by picking orders as they are submitted throughout the day. In other cases, distributors have reconfigured their order cycle to create additional time between the time orders are submitted and when they are delivered, allowing more daytime hours for order picking.
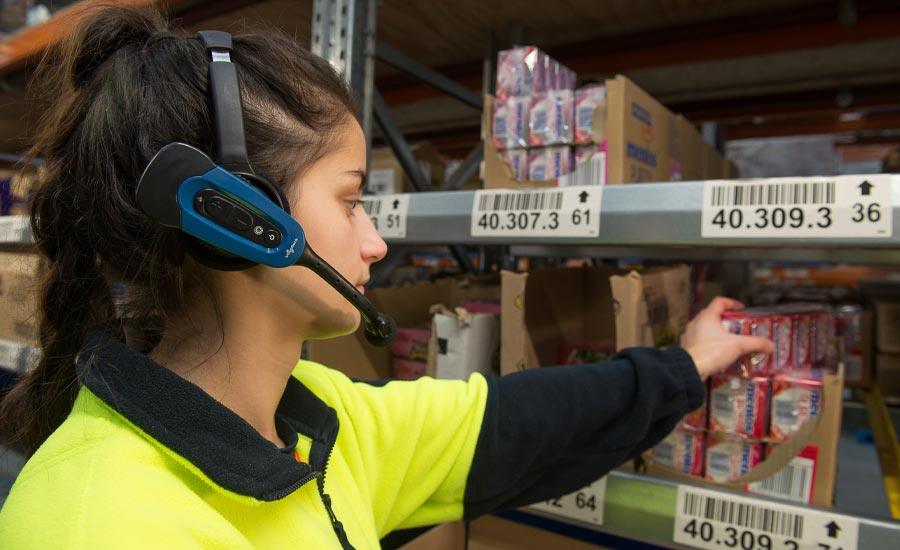
Image courtesy of Dematic
“Additionally, with the challenges in attracting and retaining delivery drivers, there is a push to create more driver-friendly and store-friendly delivery pallets,” Nevenhoven continues. “However, creating driver- and store-friendly pallets requires additional staffing requirements in the warehouse, as it generally has a negative impact on picking productivity. The combination of all of these factors is generating increased interest in automation, which can reduce the amount of staff required to accomplish picking and palletizing tasks while also facilitating the building of more stable and higher density pallets.”
Meeting market trends
As market trends have an impact on beverage warehousing, experts highlight how integrating voice- picking technologies help meet the various challenges operations are facing.
“Adapting requires a holistic view of operations and scalable technology solutions like robotics paired with voice technology,” Honeywell’s Smith explains. “Robotics and automation are sought-after solutions to address labor challenges. With numerous product options, maintaining stock is vital to meet consumer needs, especially in the context of SKU proliferation, like in the energy drink industry.
“At Honeywell, we try to emphasize technology’s application within the DC, focusing on its interaction with mobile workers,” Smith continues. “We aim to integrate technology seamlessly while enhancing mobile workers’ effectiveness. Voice technology facilitates natural interaction between mobile workers and robots like cobots, reducing travel time and improving safety and efficiency. It offers user-friendly guidance, ensuring workers are productive from day one.”
When it comes to SKU proliferation and labor challenges, Encompass’ Ray notes that voice-picking solutions are necessary to streamline operations.
“SKU proliferation has been one of the biggest market trends the industry has ever seen,” Ray says. “In addition, there are more types of beverages moving through warehouses including seltzers, kombuchas, nitro coffees, and NA beverages. The warehouse needs to manage accessible locations for rapid picking and consider incorporating warehouse automation to streamline warehouse operations.
“Voice-pick enables rapid employee onboarding, while also making the job experience a successful one for the employee and the warehouse team,” Ray continues. “Warehouse managers are not dependent on learning a product’s location and instead use the space to match product sales velocity and minimize travel time. Voice-pick provides multi-language support, so whether your employees are native English speakers or fluent in Spanish, Korean, or another language, they can be productive and increase their cases-per-hour pick rate.”
Dematic’s Nevenhoven points to increased service levels from retail environments as a trend that’s impacting picking productivity.
“Voice technologies are extending beyond picking only functionality to increase efficiency in operations such as replenishment, staging and shipping,” he says. “Additionally, integrating voice-picking technologies with varying levels of automation creates a seamless operation between manual and automated processes.”
Moving forward
As voice-picking technology continues to evolve, experts highlight how advanced technologies can offer significant advantages to beverage operations.
“Ongoing enhancements in speech recognition technology prioritize processor speed, operating systems, ‘Pick Up and Go’ speech recognition, and integrated sensors for improved data capture, ultimately boosting accuracy,” Honeywell’s Smith says. “These advancements aim for quicker startup, greater reliability, and enhanced accuracy, directly benefiting mobile workers’ daily performance.
Encompass’ Ray points to advancements in voice-picking features that work to improve efficiency and productivity for distributors.
“[Voice picking] now has features such as natural language processing, multi-language support, noise cancellation, integration with other systems, and predictive analytics,” she says. “These features and more can help improve efficiency and productivity for distributors of any size.”
Dematic’s Nevenhoven points to an evolution in the types of devices and peripherals used.
“Lower cost, consumer-grade devices are often used instead of enterprise level, purpose-built devices. New and more ergonomic scanner devices are also being integrated with voice-based solutions,” Nevenhoven says. “Additionally, it’s becoming more prevalent to incorporate a visual component into voice picking, where the instruction set communicated via voice is also displayed on the device, and tasks can be acknowledged either by voice or the touch screen on the device.”
As hands-free operation for workers enables advantages to beverage operations, Honeywell Smith notes that voice-picking technology has consistently proven its value in this domain.
“The future focus will be on expanding into additional workflows such as replenishment, restocking, and pick and pack,” he says. “Additionally, seamless integration with emerging technologies like vision picking, augmented reality, and robotics holds great promise. When combined, these trends create a collaborative robot (cobot) experience within distribution centers.
“Artificial intelligence (AI) will also play a pivotal role, offering workers insights into their progress and aiding in issue identification within the system and network. AI can even potentially perform self-healing tasks, contributing to smoother operations,” Smith concludes.