With the health and safety of consumers at an all-time high, ensuring that beverage packaging and the products within are free from contaminants has never been more important. Experts note that vision systems within packaging inspection equipment along with some “latest and greatest” technological advances in the use of artificial intelligence (AI) are facilitating breakthroughs in brand protection, reducing waste and increasing throughput.
Miles Kroner, business manager of vision and serialization at Mettler-Toledo Product Inspection, notes that the use of AI to inspect for “hard to define” defects or to inspect products with a large variability in their finished product has become more common.
“The majority of the current AI solutions available aren’t yet robust and industrialized for many applications, but some offer a nice solution for niche inspections,” Kroner explains. “There is no question that AI can be a strong inspection tool, but for implementing a robust vision inspection solution, proper lighting, precise product handling and image acquisition are still requirements for any vision solution to function well. Leveraging AI appropriately and combining with the aforementioned aspects of a vision solution is a challenge the vision industry will continue to work on for years to come.”
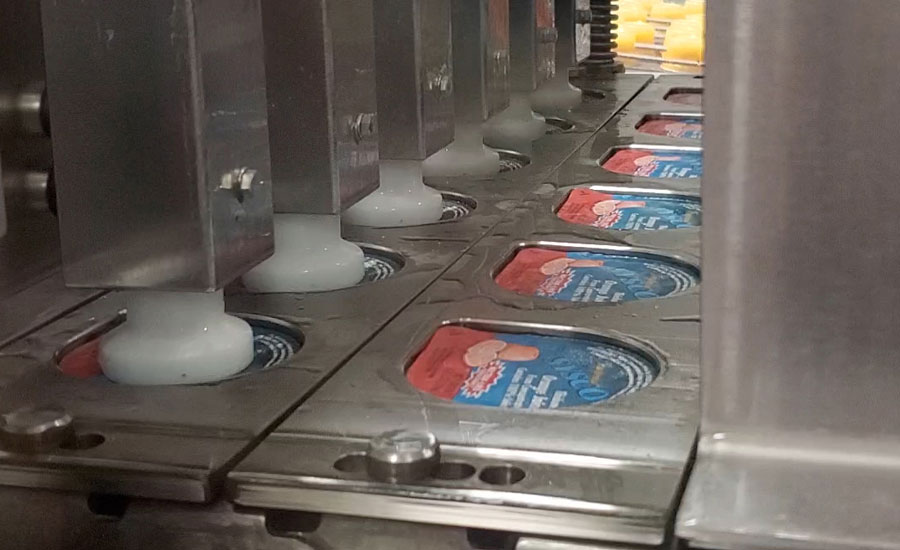
Image courtesy of Teledyne TapTone
Within the brewing industry, the Lutz, Fla.-based company is noticing a transition away from glass bottles to aluminum cans. Among the advantages of vision inspection equipment is that it eyes empty bottles and cans before filling, which eliminates defects and reduces product waste. “Production line vision inspection detects bottles with capping, label and fill-level problems before they can leave the facility,” Kroner explains.
The advent of more tall and slim cans in the beverage market is creating a need for additional inspection expertise because the popular 12-ounce cans are harder to inspect, Mark Bussard, product line manager at Falmouth, Mass.-based Teledyne TapTone, points out.
“The smaller can ends don’t deflect as much when under pressure versus when they are leaking,” Bussard says. “So the best way to inspect these cans is with the TapTone Force technology, which does not rely on can end deflection but instead takes a reading of the can sidewall to determine more accurately the pressure (or loss of) in the can.”
Additionally, because slim cans run at a higher cans per minute (CPM) threshold for the same line speed of larger diameter cans, can rejection on the highest speed lines is more critical than before. “Not only are there more cans to track, but they are a smaller target so the precision of the rejecter must meet these new demands,” Bussard says.
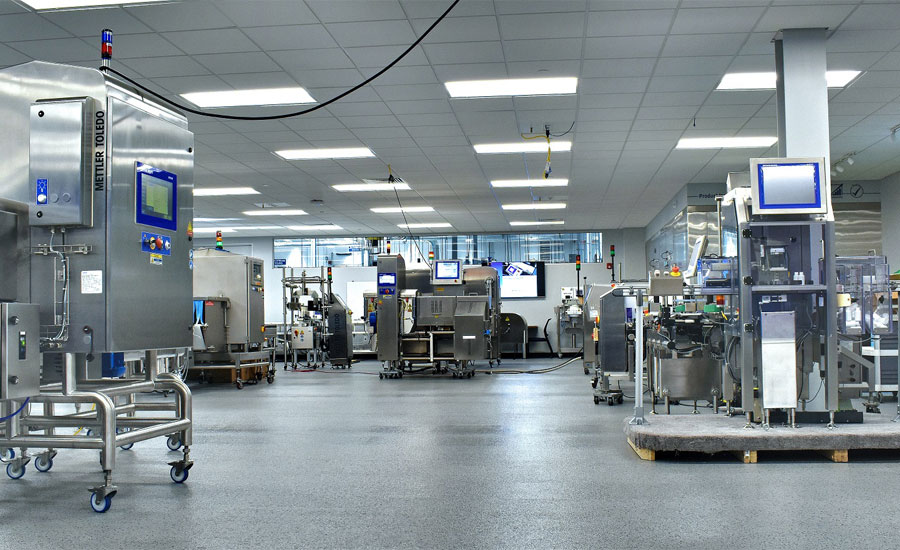
Image courtesy of Mettler-Toledo
Retrofitting requirements
Given the importance of inspection equipment to beverage operations, original equipment manufacturers (OEMs) are looking for solutions with a compact footprint, are flexible and have robust connectivity capabilities, Mettler-Toledo’s Kroner says. He also pinpoints that the equipment should be easy to integrate with the ability to be retrofitted into an existing line paramount.
Teledyne TapTone’s Bussard expresses similar sentiments: “They are constantly asking for inspection equipment to meet the line speeds of the new higher speed lines with the ability to also inspect a large variety of container types, sizes and shapes. They want system with the flexibility to handle these variables with the least amount of changeover requirements,” he says.
Because sustainability remains a hot-button topic in the industry, the push toward eco-friendly packaging options and the trend to move away from single-use plastics and toward aluminum in the beverage market is impacting inspection equipment ― but not the equipment design, Bussard says.
“It has made a shift in the types of inspection, which is now more popular than just a few years ago,” he says. “It has not changed the equipment design but simply increased the volumes of the style equipment being purchased.”
TapTone offers a full line of Leak Inspection, Fill Level, Seal Integrity products for post fill and seal applications. The company’s equipment also supports multiple sensors from a single controller and performs additional inspections such as cap placement, foil detection, missing vent tube, label inspection as well other various inspection needs.
“TapTone solutions are designed to meet the highest speeds of today’s production. These systems are capable of performing inspections on a wide variety of container types, HDPE, PET, aluminum, glass, steel, paperboard cartons and more,” Bussard says. “Leak inspection and fill level can be performed at full production speeds for pressurized and non-pressurized containers. The TapTone solutions are designed to have minimal impact on the line as they are cantilevered over the existing conveyor and use up the absolute minimum floor space, allowing inspections to be added where they are best performed on the line.”
A vision for the future
The vision inspection industry continues to leverage advancements made in the computing, camera, vision inspection software and lighting worlds, leading to faster, more powerful and easier-to-use vision systems, Mettler-Toledo’s Kroner says.
Among the brand protection industrialized vision systems the company offers are label, package, cap and seal inspection to check for almost any defect on product packaging to ensure that every item meets brand owners’ stringent quality standards to always present a perfect product to market.
Upfront, automated vision inspection systems also can catch product and fill defect mistakes early on, which means “fewer errors to proliferate in production, and any errors are fixed or rejected easily,” Kroner says.
Advancements in inspection software also is increasing productivity while reallocating costly manual inspection. “Intuitive software such as Mettler-Toledo’s CIVCore allows for easy product changeovers, simplifies user management and provides valuable production data that can be used to improve production processes,” Kroner says. “… Mettler-Toledo customizes solutions that address unique conditions. Our open interfaces such as OPC UA support Industry 4.0 initiatives, enabling production data to be accessed, analyzed and controlled anytime and anywhere.”
In addition to software improvements, Teledyne TapTone’s Bussard notes that inspection equipment will continue to be refined and improved to keep up with the higher speeds of the newer lines being installed. “The need for data collection and networking of the systems is an ever-growing requirement. These production statistics are critical for maximum optimization of the production as well used for predictive maintenance,” he says.
He also notes that simply identifying bad products is just one part of the equation. “[We need] the means to reject it off the line. While this is less complicated than the inspection itself, there often needs to be unique methods developed for effective and reliable rejection,” Bussard says.
Mettler-Toledo’s Kroner predicts that AI will play a larger role in the inspection systems of the future. “As AI solutions improve and become more industrialized, stable and refined, AI to inspect for ‘hard to define’ defects or to inspect products with large variability in their finished form will become a more valuable tool.”