For 10 seasons, the reality TV show “Clean House” helped families clean up the clutter that inflicted their homes. Originally hosted by Niecy Nash-Betts, the episodic structure showcased the extent of the clutter, gathering items to sell at a yard sale and using the proceeds to makeover the home and a final reveal to the family. Part of the makeover also includes organizing of the items the family held onto to transform closets, garages, offices and more.
Beverage warehouses don’t have the benefit of a makeover and design show to help streamline their operations when portfolios get out of hand. Instead, they are turning to the latest in storage systems to ensure all is in working order.
Kyle Nevenhoven, head of solution consulting Americas and global solutions standardization at Dematic, Atlanta, notes that historically beverage warehouses were designed to store a limited number of SKUs, but in large quantities. As SKU proliferation has escalated over the years, the strain on storage has become evident, resulting in a new approach to operations.
“As SKU proliferation became more impactful on warehouse operations, the first approach was the introduction of different types of racking systems, such as single select pallet racking, double deep pallet racking, and push-back racking,” Nevenhoven says. “All of these types of racking systems allow for the storage of a larger SKU portfolio, increase SKU access, and increase total storage area utilization. With the increase in varying types of storage locations with different capacities and storage parameters, warehouse management systems became a necessity to manage the storage locations and the various attributes of the stored SKUs.”
Nevenhoven adds that racking systems have benefited warehouse, but as SKU proliferation continues, distribution centers (DCs) have realized the benefits of automated storage and retrieval systems (ASRS). “These automated storage systems have been designed to store SKUs at pallet and case levels,” he says.
Josh Goodman, AIA and principal at HDA, St. Louis, explains that when accommodating SKU increase, it’s important implement better storage methods because “simply expanding a building footprint does not solve the entire impact.”
Yet, storage systems go beyond simply storing product, but allow for improved organization and efficiency.
“Storage systems allow products to be cataloged and stored based on volume and delivery method,” Goodman says. “High volume and low volume products can be located in the most efficient location for storage, order picking and refilling.”
Ryan Smith, vice president of automation at Westfalia Technologies Inc., York, Pa., elaborates on how ASRS platforms are equipped to accommodate an influx of SKUs.
“First, a design that incorporates the ability to change lane depths of storage lanes can help increase the number of lanes available for high moving product and increase the number of lanes available for slow moving product,” he says. “Westfalia has a unique solution for this by using ‘shared middle blocks’ to allow operators to configure the warehouse to their current needs. Another innovation that cannot be ignored is a solid warehouse management system that allows the operation to maximize the pallet utilization of the system through intelligent SKU mixing.”
Although Smith has illustrated the ways that ASRS can help address SKU proliferation, he notes that supply chain issues in recent years resulted in a reduction of SKUs.
“During the post-COVID supply chain challenges, we actually saw a reduction of SKUs with bottlers and manufacturers as they focused more on their high moving product,” he says. “As those challenges were solved, we have seen the number of SKUs steadily increasing to their pre-COVID levels.
“However, we do see some distributors challenged by SKU proliferation through the acquisition of new product lines, and if they are not prepared, it can be disastrous,” Smith continues. “Careful planning and understanding what adding additional SKUs to the DC should be analyzed and solved before the product arrives at the receiving dock.”
Yet, SKU fluctuations is just one trend impacting storage accommodations in beverage warehouses. Like many industries, labor shortages also are impacting storage operations.
“The labor shortage has had a tremendous impact on the beverage industry,” Smith says. “Order selection for the beverage market is often labor intensive and the need for automation is increasing to provide some relief.”
Dematic’s Nevenhoven echoes similar sentiments. “Not only is it difficult to find and retain labor, but the high turnover caused by the competitive labor market leads to less experienced operators running fork truck equipment,” he explains. “This increases the likelihood of causing property and product damage.”
Another trend in the beverage market has been mergers and acquisitions of distributors.
“Continued consolidation of distribution networks has put additional pressure on storage systems, increasing the overall storage requirements and the number of SKUs to be stored,” Nevenhoven says. “When distribution centers are consolidated, they often need to store more inventory than they were originally built to accommodate.”
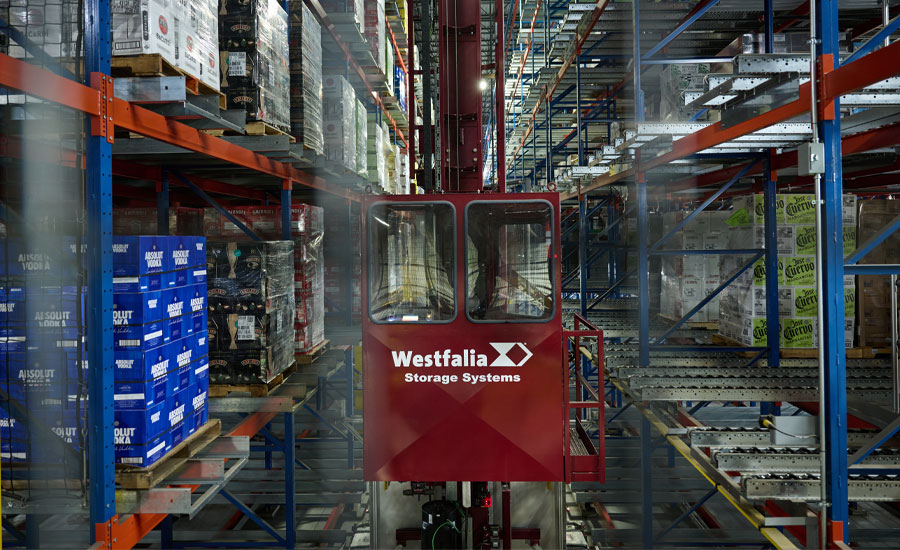
An automation love story
Automation and warehouses might seem synonymous to many nowadays, but the union of automation and beverage facilities has shown the story arc of a rom-com: slow beginnings, but destined to happen.
“Storage automation technologies have been present in distribution centers for many years, but the introduction of these technologies into beverage distribution centers has just started to gain momentum over the last five to 10 years,” Nevenhoven explains.
He then elaborates on the impact that automation can have on a beverage distribution center.
“The ability to store pallets more densely, and often in taller buildings than can be utilized with manual storage systems, allows for the introduction of higher SKU counts,” Nevenhoven explains. “It can also ease the expansion requirements brought on by acquisition and consolidation. Storage automation is well suited to store pallets with precision, maintain date code integrity, and remove the likelihood of product and property damage.”
HDA’s Goodman adds that beyond the storage benefits, automated systems can improve warehouse performance.
“Depending on the level of automation, some levels of human error are lessened or eliminated. Inventory rotation, to replenish products based on their production date, is managed by larger advanced systems,” he says. “HDA is currently looking at including 7-high storage for one of our clients, which is approximately 75 feet of clear height. Because this client has had extensive SKU proliferation, they need to expand.
“As a result of automation and storage system innovations like 7-high storage, this allows them to significantly cut down on the square footage required for the addition,” Goodman continues. “Usually, we design 4-high storage, so this is a big jump from where most wholesalers are right now.”
Westfalia’s Smith also notes the larger role automation is playing in warehouses, in terms of storage and other ancillary benefits.
“By utilizing an ASRS, a distributor can improve receiving times, automate the entire replenishment process, and make the picking process more efficient for the pickers,” he says. “There have also been huge strides at making automating layer picking and palletization more achievable than ever before.”
Given all this, Smith expects to see automation to be a key focus for the future of warehouse operations.
“We foresee more automation in general within the beverage industry for the next few years,” he says. “With the ongoing labor shortages, it is more important than ever to make sure that you have the most efficient automation systems in place to maximize the number of cases that you can ship each night.”
Dematic’s Nevenhoven also remains optimistic about automation’s place in beverage warehouse and the technology driving that arena, particularly pallet shuttling.
“Pallet shuttle technology has matured significantly over the past few years and can be a great choice for beverage operations,” he says. “This is particularly impactful for those that are looking to add an automated storage system to an existing building or those that are in areas that cannot build high bay warehouse storage systems. Pallet shuttle systems are extremely flexible in handling a wide range of SKUs in a very dense manner.”
HDA’s Goodman also expects to see increased options for storage system solutions as this market evolves. “Many new systems will be available based on the type and volume of product, which can more efficiently store and distribute the specific product,” he says.
With an eagerness to solve the complexities of beverage warehouses, the marriage of automation and storage systems are sure to stand the test of time.