A staple of family reunions, school field days and summer camps, the three-legged race features pairs of runners where the left leg of one runner and the right leg of the other are strapped together, forcing the two to keep pace with one another to ensure they finish and hopefully win the race.
In beverage warehouses, the rise of automation has prompted various operations to continue to make advancements to equipment to ensure that the speed and pace are in sync and processes are running efficiently.
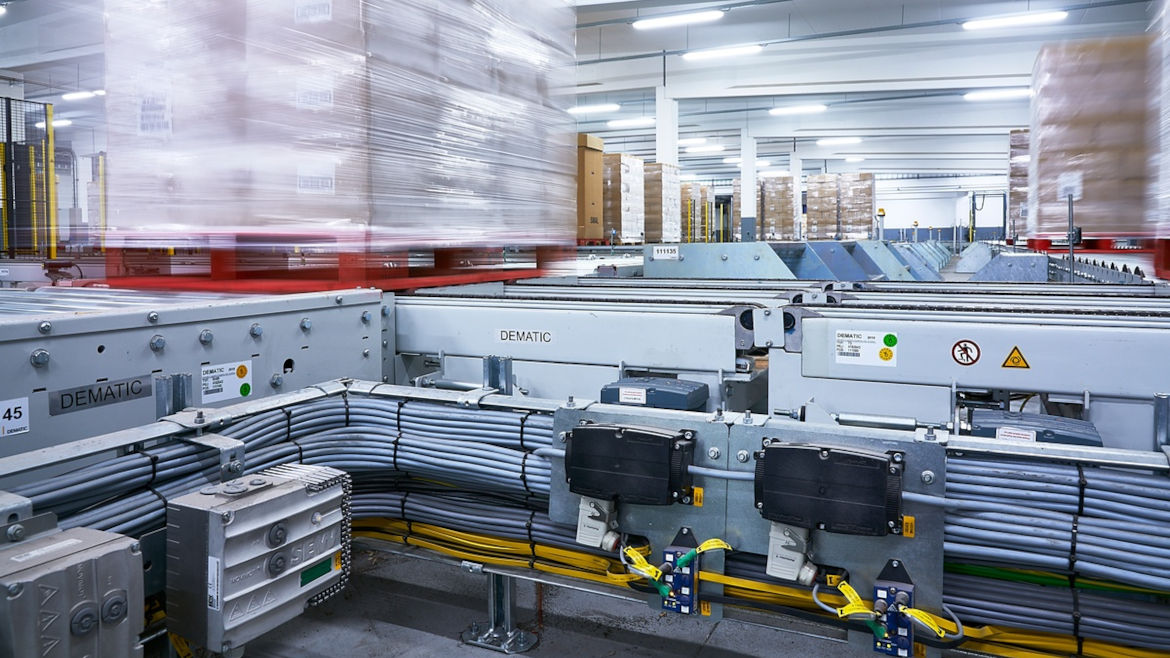
“While automated solutions such as AMRs are growing in popularity, the conveyor market must match pace by making advancements toward improving flexibility, scalability, conveyor controls and materials, as AMRs remain advantageous in a world where space is a premium,” says Brandon Duba, solution consultant at Dematic, Atlanta.
Duba explains that conveyors’ reliability in beverage operations has been proven thanks to their ability to move large heavy cases, but as integration of other automated solutions proliferate, conveyors also are seeing a steady increase in usage.
However, integration with other automated solutions is not the only item driving conveyor solutions. Given the innovation throughout the beverage industry whether it be packaging or new products, original equipment manufacturers (OEMs) are taking these trends into account with their latest solutions.
“Beverage packaging proliferation demands conveyor adaptability,” Duba says. “With ever-changing pack sizes and types, the conveyor market must be able to safely handle flexible pouches without causing damage to customer-facing products, while still efficiently transporting materials across the warehouse.
“This drive to innovate requires modifications including smaller roller centers, compact conveyors, and distinct surfaces to handle the delicate packaging,” he continues. “With a larger portfolio of conveyors, distributors will have more options to better suit their solution needs.”
Duba explains that order profiles on average are including more SKUs in each order and fewer cases in each line. This has led to greater complexity for conveyors.
“SKU proliferation therefore creates a requirement for an increased number of pick locations as well as the growth of conveyor systems,” he says. “Sorting technologies need to adapt to handle higher throughputs as space utilization quickly becomes consumed and routing becomes more convoluted. Distributors and retailers must consider technology that can be scaled according to their needs.”
This is prompting beverage manufacturers and distributors to seek out cost-effective solutions that can accommodate the growing SKU environment.
“Utilizing conveyors to transport cases, pallets, and shippers we can design highly automated solutions in a compact and efficient manner,” Duba says in regards to Dematic’s solutions. “We are asked to design automated solutions and, in doing so, we recognize that a conveyor can play an integral part in a solution’s design while not being a complete solution on its own.”
Next steps
As OEMs keep an eye of the evolutions in the beverage market, companies are turning to the latest innovations to steer future conveyor solutions.
“The implementation of artificial intelligence (AI) could greatly improve conveyor equipment,” Duba says. “AI can adjust conveyor-based settings to reduce bottlenecks and improve throughput capacity. These setting adjustments might also provide a more sustainable type of product to ramp down equipment when possible, resulting in less wear-and-tear and reducing the amount of power used to operate.”
Duba adds that AI’s benefits can extend beyond operational, offering benefits when it comes to maintenance procedures.
“AI’s ability to identify errors would use data based on real-time equipment to provide more detailed maintenance schedules and reduce downtime,” he explains. “Machine vision is another form of technology that could be used to identify and remove SKU labels that are scanned for sorting or routing processes.”
Beyond the potential of AI, Duba prognosticates that conveyors will be a key piece of the automation process going forward.
“Conveyors will also become more closely integrated with other pieces of automation to provide operators with a seamless and self-reliant solution,” he says. “They will be able to feed articulating robotic arms, deliver material to and from self-guided vehicles, sort packages by order or destination, and provide operators with ergonomic means of pick and pack.”