In the realm of physical fitness, research has shown that stretching can improve flexibility. For example, in its “Benefits of flexibility” article, Harvard Health Publishing notes that “a well-stretched muscle more easily achieves its full range of motion.”
Similarly, experts within the beverage industry often note how flexible packaging equipment can help achieve a full range of motion, with case packing and wrapping equipment being no different.
“The retail market is a major driver in case packer flexibility,” says Peter Fox, CEO of SOMIC Packaging Inc., Eagan, MN. “The efficiency of having one case packer with the capability of running the various primary package is driven by practicality and efficiencies.”
Moreover, Fox notes that with case packing requirements changing in the number of formats required, retailers are looking for multiple size offerings on the shelf.
“Club stores and retailers often demand a unique presentation of the product on shelf,” he explains. “This means that in addition to case count versatility, the case packers must also have the flexibility to run display trays for club, or unique, retail-ready options for retailers such as Aldi.
“Having a case packer that can package the various primary package beverage formats may also be a factor,” Fox continues. “From stand-up pouches and PET/glass bottles to aluminum cans, having the versatility to handle various containers is a valuable option.”
David Nettles, vice president of sales at Washington, MO-based Texwrap, a ProMach product brand, points to the need for flexible equipment to produce more packaged products with less maintenance and fewer line resources.
“The ability to changeover quickly and accurately is key to prevent lost production due to mistakes or lengthy changeover processes,” Nettles says. “Customers need fast speed to achieve high output and competitively market their products and services.
“The ability to run more containers and different formats of those containers is key, especially for contract packagers, as they tend to have more diverse requirements,” he continues.
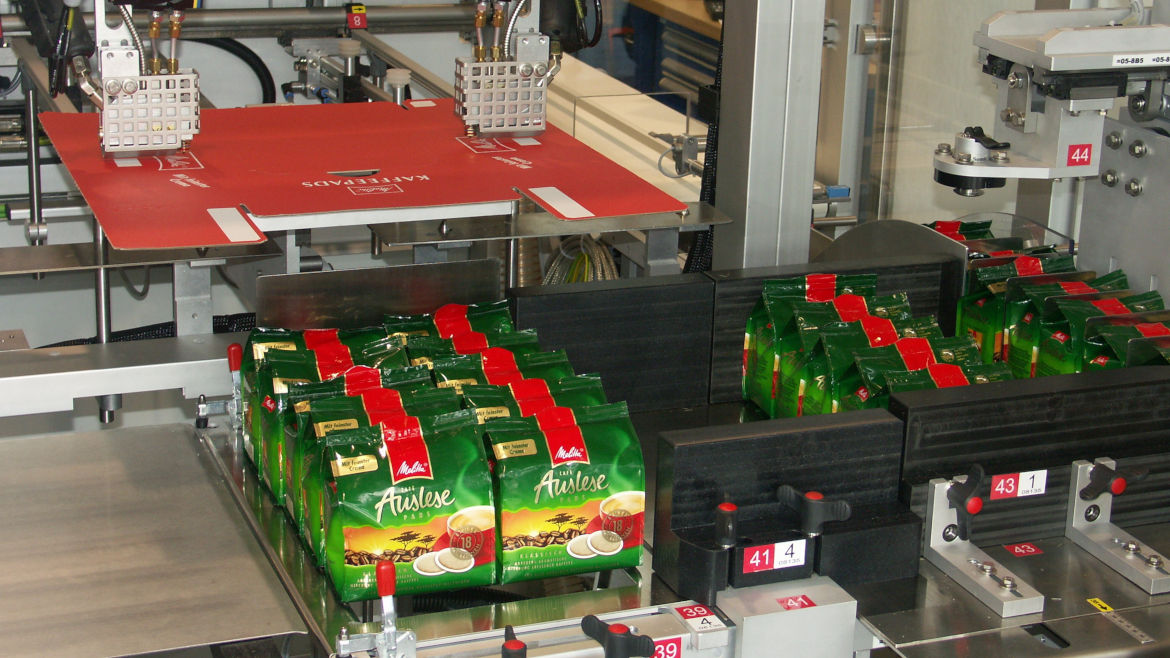
Image courtesy of SOMIC
Meeting beverage market trends
Aside from the need for flexible equipment, experts note that sustainability trends are impacting case packers and wrappers within the industry.
“Container materials, construction and shapes are evolving in efforts to make packaging more sustainable,” Texwrap’s Nettles says. “For example, container wall thickness is being reduced to cut down on material used, but this can have an effect on product handling. Machines need to be able to accommodate these thinner materials.”
SOMIC’s Fox points to the use of alternative primary packages, such as pouches, as having a significant impact on case packers that are designed to run cans or bottles.
“Running flexible formats on the same case packer used for rigid containers is typically difficult or impossible on most machines,” he says. “Given the modularity of the SOMIC case packers, this can be achieved by quickly and effectively changing the infeed and collation module.”
Meanwhile, the developing trend of eliminating shrink wrapped trays also is impacting packers and wrappers, Fox says.
“This package style could be replaced with a display tray and a corrugated cover to contain the product,” he explains. “The cover could be constructed from recycled corrugated on unprinted material, making recycling easier. In addition to the material, the energy consumption of shrink wrapping systems is substantial.
“Eliminating the shrink wrap heat tunnel would save a significant amount — as much as 80% — of energy consumption in the packaging operation,” Fox continues.
Among other beverage market trends affecting packers and wrappers, Fox points to the use of non-traditional packaging, such as pods.
“While beverage pods are not necessarily new to the market, packaging of these formats is radically different than a traditional beverage package because these types of delivery systems require a completely different approach to case packing,” he says. “The small capsules require very precise handling due to the tiny primary package, and product manipulation is necessary to assemble an efficient case or carton configuration.”
Keeping up with versatility
As suppliers work to handle a wider project scope in case packing and wrapping, experts highlight the typical requests from small to midsize to larger beverage operations.
Texwrap’s Nettles notes that, in general, beverage operations have fewer resources available, “so the ability to provide a turnkey system is an ever-increasing value.”
As far as requests for equipment from small to midsize operations, Nettle points to the need for a lower speed rating with reduced component and electrical specifications. This, however, differs beverage operations on a larger scale.
“Larger operations tend to demand more components and extensive electrical specifications as they attempt to streamline their supply chain,” he explains.
SOMIC’s Fox points to requests for versatile equipment that meet small to midsize operational needs.
“A medium to small beverage packer is typically looking to have single lines that can handle a wide variety of package and case formats,” he says. “With future unknown options, they are required to stay nimble.”
By comparison, Fox notes that larger beverage packers usually look for high speed dedicated case packers. “While these machines provide the speed and efficiencies that are required, long-term versatility is extraordinarily limited,” he explains.
Looking toward the future of case packing and wrapping, Texwarap’s Nettles anticipates that artificial intelligence (AI) will significantly impact packaging systems.
“The ability for a machine to diagnose, learn from and predict events has a great impact on the value for a packaging system, making it able to run more independently with fewer downtimes,” he says.
SOMIC’s Fox, echoes similar sentiments, noting how AI could impact machine learning and machine reaction to changing conditions on the machine.
“Those conditions include machine responses to varying material conditions, such as warped corrugated or having the machine automatically adjust to the variation,” Fox explains. “Product infeed changes requiring the machine to ramp up or down would also benefit overall efficiencies and the lifecycle of the machine components.”
Although flexibility might be driving case packing and wrapping equipment today, AI might be the next must-have from original equipment manufacturers.