The quote “A goal without a plan is just a wish” often can be found on inspirational signs or even email signatures. As industries throughout the supply chain strive to create a more sustainable future, these players are laying out clear plans to make this goal more than a wish.
The plastic bottle market is among the industries that have taken great steps to reduce the amount of materials used. Now the industry is playing an active role in utilizing more sustainable materials.
“With the rising consciousness for protecting the environment and the regulations for plastics, beverage players are adapting their packaging as well as their production line,” says Francesca Bellucci, sustainability portfolio director for Sidel, Norcross, Ga. “For instance, the European Union created the European Green Deal, and one of its key blocks is the Circular Economy Action Plan. One of the famous directives is the single use plastics (SUP), which sets clear targets to implement mandatory tethered caps for all beverage containers up to 3 liters by 2024; as well as at least 25% recycled PET (rPET) content in plastic containers by 2025, and 30% recycled content in all plastic containers by 2030, together with a collection rate of 77% for all single-use plastic beverage containers by 2025.”
These efforts also are having a butterfly effect on the manufacturing equipment.
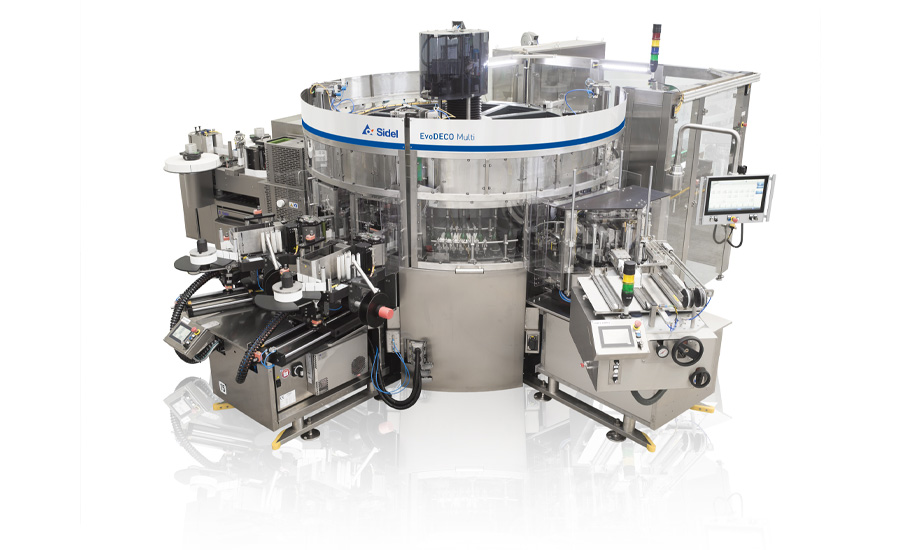
Image courtesy of Sidel
“Therefore, plastic bottle manufacturing equipment needs to be ready to handle growing percentages of recycled content and to deal with tethered caps without any loss in quality or performance,” Bellucci explains. “The circular economy concept is not only an EU initiative, but also part of worldwide momentum in this direction. It is now in companies’ hands to transform the regulations into business opportunities.”
Jon Larson, head of plastic technology sales for North America at Krones Inc., Franklin, Wis., echoes similar sentiments regarding the ripple effect of sustainable packaging improvements on the manufacturing end.
“Sustainable packaging efforts have different influences on the plastic bottle manufacturing equipment,” he says. “Declining volumes due to plastic bashing are not a good situation for spending much money, as well in the [research and development] (R&D) sector. On the other hand, plastic bottles, done well, are one of the most sustainable possible [packages]. There are many LCAs (life cycle analysis) available supporting that.
“Paramount are good waste management together with high recycling rates,” Larson continues. “Also, legislative support like the new EU SUP (European Union single-use plastics) directive help developing in the right direction. The problem with plastic packaging mainly begins when it is lost and littered into the environment.”
Larson explains that equipment has been developed to support these positive trends and necessities, including lower packaging weights, lower energy consumption, lower emissions, and higher post-consumer recycled (PCR) content and tethered caps.
As PCR content becomes more highly utilized by beverage-makers, operations managers will need to ensure that their equipment can handle this evolution.
“The beverage-makers will have to keep their equipment up to date and to comply with the corresponding legal framework,” Larson says. “An eye has to be kept on the quality of the material for the corresponding processes. Quality of the collected post-consumer material for the recyclers, quality of the rPET material for the preform producers and quality of the preforms for the bottle producers. The necessary specifications and material constancy have to be ensured.”
Although materials like rPET are among the vanguard solutions, Sidel’s Bellucci notes that it remains important that efficacy remains intact.
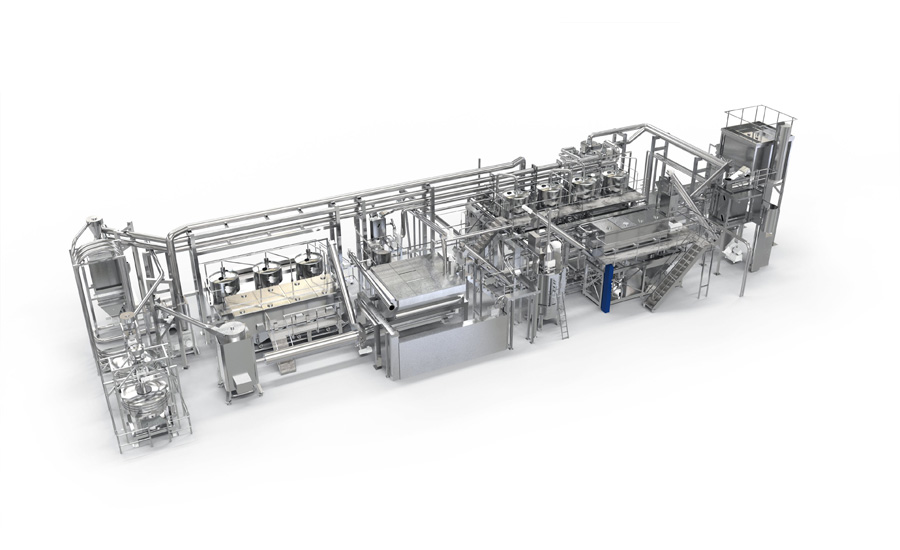
Image courtesy of Krones Inc.
“The quality of food grade rPET varies considerably according to the collection method, the product mix in the collection and the history of the bottles,” she says. “In 2019, Sidel implemented a qualification protocol for rPET content, to help promote the development of rPET bottles in the market in line with the requirements of the European SUP directive and brand owners’ own commitments to adopt rPET. Additionally, Sidel’s blowers are ready to handle up to 100% rPET content, and we offer services to make existing lines suitable for it.”
Bellucci further emphasizes the efforts by the company to support these sustainable measures within the packaging materials market.
“Trends such as tethered caps, rPET, bottle lightweighting, usage of recycled materials across primary, secondary and tertiary packaging are all tightly bonded with sustainability, as they reduce the carbon footprint and are in line with the circular economy,” she says. “In respond to these trends, Sidel’s X-LITE Still is an extremely lightweight 500-ml PET bottle that is compatible with tethered caps and 100% rPET, with reduced costs and impact for the environment.
“Another is AYA, an eco-friendly end-to-end packaging concept, which was awarded ‘Best Drink Packaging Design’ at the World Food Innovation Awards 2020,” Bellucci continues. “Our overwrappers and case packers are also able to handle 100% recycled materials, both plastic and cartons.”
And Bellucci prognosticates that sustainability goals will only continue to have an increasing impact on the machinery for plastic bottle manufacturing.
“In the future, the manufacturing equipment will be obliged to follow the upcoming sustainability regulations,” she says. “It is crucial to reduce greenhouse gas emissions, water and energy consumption and waste, without compromising on the performance or aesthetics of products, creating perfect marriages of form and function.”
Krones’ Larson notes that given these materials evolutions, it will remain important for beverage manufacturers to consider a broader timeline when investing in packaging equipment.
“As always TCO (total cost of ownership), OEE (overall equipment efficiency) and flexibility are paramount,” he says. “The equipment has to be ‘sustainable,’ in that sense that it not only has to make today’s job, but also can cope with possible challenges to come tomorrow. That means a big advantage for the well-established machine suppliers that will also be there tomorrow when new challenges have to be met and solution suppliers partner with their customers to successfully master these challenges.”
Future factors
Although sustainable packaging goals has been one of the largest factors influencing plastic bottle manufacturing, experts recognize it’s not the only influence of today.
Like many industries, the pandemic has seeped into the supply chain for original equipment manufacturers.
“The global pandemic has affected the packaging solution industry by leading to a significant price increase and shortage of raw materials and components used in packaging equipment,” Sidel’s Bellucci says. “The COVID-19 pandemic including additional factors, have created a drastic shortage of raw materials (including most of metals) and components such as microchips, semiconductors, and other components.
“This shortage is an outcome of supply-related disruptions, including forced closure of factories, together with an unanticipated increase in demand for many goods and specifically for personal electronics such as cell phones and laptops as people were required to work or study remotely,” she continues. “Those factors have hardly affected the packaging solution industry by leading to a significant price increase combined with longer lead times.”
Another influencer on the packaging equipment market is adoption of digitalization. This is something Krones is tapped into, in fact, a study undertaken by CAPITAL and Infront Consulting analyzed digital transformation in Germany’s largest companies and ranked Krones AG among the champions of digital transformation, Larson notes.
“The use of AI to improve production safety add OEE, the digital monitoring of the complete machine and product lifecycle and not least the guarantee of data safety in the context of this all will be part of our work also in the future,” he says.
Efforts by original equipment manufacturers suggest that this industry is ready to support trends driving plastic bottle manufacturing.