A July 2022 blog post on Runtastic.com offers a slew of tips to help runners increase their stamina and endurance. The No. 1 item stressed was consistency with three to four sessions a week at 30 minutes or more ― highlighting that speed will follow endurance. Like the marriage of endurance and speed in a running regime, beverage packaging and manufacturing operations have married speed and accuracy to inspect and protect today’s beverages.
“As food safety regulations and technology has evolved, so has inspection equipment,” says Sarrina Crowley, marketing communications manager at Mettler-Toledo Product Inspection, Lutz, Fla. “Today’s systems can inspect more accurately, at faster line speeds, with fewer false rejects.”
Keri Klein, product line manager of checkweighing and vision at Mettler-Toledo Product Inspection, echoes similar sentiments regarding how beverage manufacturers have greater inspection abilities at faster speeds.
“Many beverage producers are looking to increase throughput while also adding inspections and/or enhancing their current inspection capabilities,” Klein says. “Mettler Toledo Product Inspection is evolving to do more and at a faster rate.”
Crowley elaborates on the inspection solutions that Mettler Toledo offers to beverage-makers in a variety of applications and environments.
“Mettler Toledo offers a very wide range of metal detectors, checkweighers, X-ray and vision inspection systems for all types of applications and environments, from dry powder additives to beverages, piped liquids, and packaged beverages in all types of containers. The addition of multiple combination systems is also a key enhancement to manufacturers. Mettler Toledo offers combinations of any types of technologies, including up to four-in-one.”
Crowley notes how offering a wide range of solutions can ensure the best solution is available to a specific application.
“For example, if a line needs to inspect for metal only, a metal detector is the best solution,” she says. “If additional contaminants could be an issue such as glass, an X-ray may be the most suitable.”
Jordan Davis, product line manager of metal detection at Mettler-Toledo Product Inspection, notes that it also can by necessary to utilize a metal detector and X-ray inspection.
“Sometimes having both technologies are warranted,” Davis says. “Particularly in piped applications, a metal detector can detect smaller contaminants than an X-ray system.”
Crowley further elaborates additional ways that inspection amalgamations can support beverage operations.
“In cases where weight inspection is needed along with other inspections, Mettler Toledo offers combination systems that take up less line space and often can be operated by a single HMI,” she says. “If a manufacturer has requirements for customized material handling, having a partner that also has this capability is helpful. Additionally, companies with global service capabilities and local field support are important when looking for a true partner.”
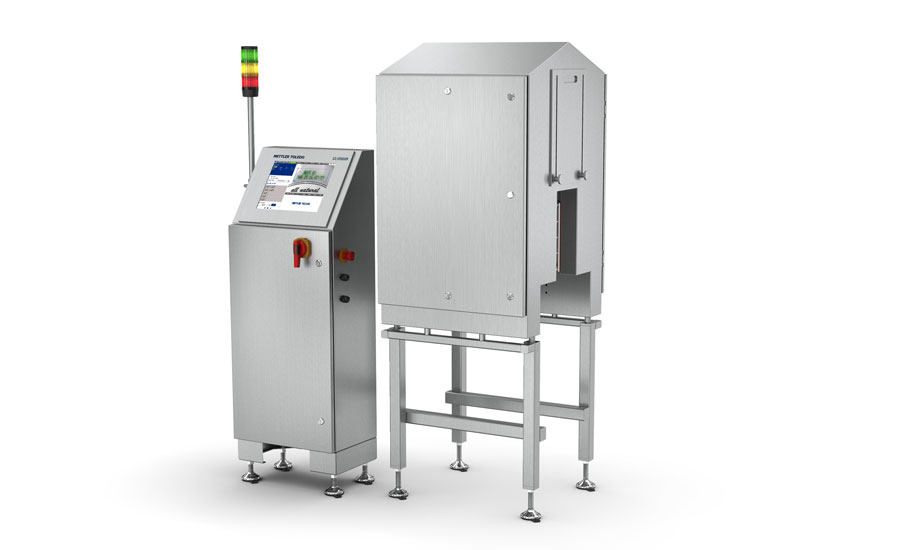
Image courtesy of Mettler-Toledo Product Inspection
Shaped for protection
As SKU proliferation has prompted the need for fast, accurate inspection systems, original equipment manufacturers also have seen beverage-makers turn to proprietary packaging to stand out on the shelf. This aspect also is impacting the future of inspection equipment.
“Product handling needs to be able to transport a wide variety ― different sizes and shapes ― potentially impacting conveyor designs,” Crowley says.
Klein highlights how Mettler Toledo’s portfolio also features add-on to support the success of product transfers, sorting and collection.
“The use of square/rectangular packages versus round may impact the type of system we recommend but will not impact the ability to inspect,” Klein says. “For vision inspection, packaging greatly impacts the inspection criteria and set-up. To address this, Mettler-Toledo has developed an intuitive tool-based software that allows customers to set-up new product recipes themselves. Therefore, when marketing creates a new package, operations can easily set-up a new product recipe on their vision system.”
Crowley also emphasizes vision systems to inspect any type of container, including oriented packages, round un-oriented packages.
“Systems can inspect for virtually any portion of a label, regardless of its location, simultaneously for safeguarding against recalls,” she says. “Systems can also check empty containers for any defects, including cap skew.”
Geri Foley, product line manager of X-ray inspection at Mettler-Toledo Product Inspection, also highlights how X-ray inspection systems can support a variety of beverage package types.
“[T]he X37 Series of X-ray inspection systems are ideal for beverages in a variety of package types including glass and are capable of simultaneously performing many quality control checks, such as assessing the fill level of products, measuring head space, detecting missing caps on plastic bottles, identifying agglomerates such as flavor and powder lumps, confirming the presence of a vacuum and inspecting for packaging defects,” Foley says.
With all these advancements in inspection equipment, experts note that more, including artificial intelligence (AI) is still to come, but still is in the early stages.
“AI is used in vision Inspection technology and will be the future, but it’s not quite production ready,” Klein says. “It requires additional development to provide end customers the ability to troubleshoot, diagnose and resolve issues on their own.”