In “Star Wars: Episode II – Attack of the Clones,” Jedi Padawan Anakin Skywalker, along with Senator Padmé Amidala, venture to the desert planet of Geonosis to save Anakin’s master, Obi-Wan Kenobi, who was captured by Separatists. While on the rescue mission, Anakin and Padmé wind up in a droid factory, where they fall onto an assembly line and must dodge the dangerous equipment.
The conveyor system on the line were used to quickly and efficiently produce droids for a galactic battle. In the beverage industry, the conveyor system market has been impacted not by Star Wars, but by the proliferation of packaging formats.
Kyle Nevenhoven, principal consultant, food and beverage, for Atlanta-based Dematic, says the proliferation of packaging formats has influenced both the conveyability and durability of cartons —changing the way conveyors are being used in the beverage world.
“Regarding general conveyability, the wide range of carton sizes and formats has required the use of conveyors with smaller rollers that are placed closer together, or in some cases, the use of belted conveyors in place of roller conveyors,” he explains. “The trends regarding reduced packaging material costs, sustainability and innovative packaging have typically negatively impacted carton durability.”
Nevenhoven notes that this “necessitated a change,” going from the traditional use of low- or zero-pressure accumulation to that of zero-contact accumulation.
“Zero-contact accumulation ultimately provides the most gentle carton handling, largely mitigating carton damage and avoiding jambs from side-by-sides,” he explains.
The consolidation of beverage wholesaler operations also has influenced the conveyor market in what he considers to be “an interesting way.”
“Traditional convey and sort systems may no longer be sufficient to accommodate the volumes, SKU complexity and labor availability challenges of larger distribution facilities,” Nevenhoven says. “Conveyor remains a vital part of beverage distribution center automation; however, it is, in many cases, no longer the primary content, but instead serves as the ‘glue’ physically interconnecting other automation.”
Earlier this year, Hartland, Wis.-based Dorner revealed a new DCMove Belted Conveyor. The conveyor “fits accuracy demanding application, such as labelers, printers, side transfer sortation and restricted spaces, in addition to packaging, eCommerce, logistics and general material handling,” the company says. The conveyor’s paint steel frame supports the right amount of strength and agility for material handling applications, it adds.
This new system is just an example of how conveyor manufacturers are working to meet the demands of beverage-makers. Dorner also released a 2700 Medium Duty Conveyor, which the company says “hits the sweet spot” between its low profile 2200 and 3200 heavy duty platforms. The conveyor is engineered to safely convey as much as 150 pounds.
Nevenhoven notes that some requests from beverage manufacturers and distributors are more common than others, but these requests are not always for conveyor systems.
“The requests received from bottlers and distributors tend to be requests for a solution that satisfies a problem statement or set of requirements, rather than requests specifying a solution type,” he says. “While [the] conveyor is likely to be the backbone of the solution, it has become increasingly rare for a bottler or distributor to specifically request a conveyor solution.”
Moving forward
As far as technological advancements go, Nevenhoven says conveyor systems have had to evolve alongside ever-changing packaging formats.
“Many of the recent advancements have been in the ability to handle smaller SKUs that may have been very difficult to handle with older conveyor technology,” he explains.
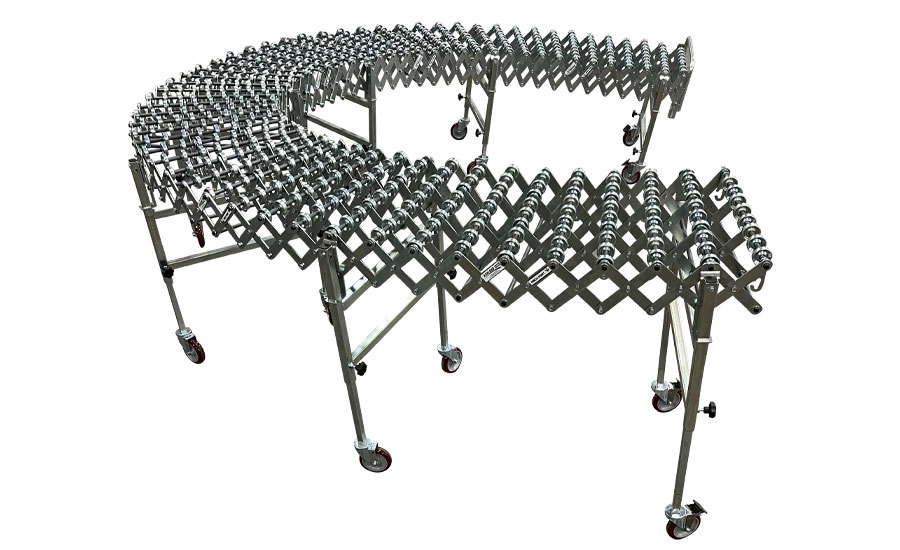
Image courtesy of ProVeyance Group
Conveyance component manufacturer ProVeyance Group recently introduced its FlexExtend Conveyor System. The company describes the system as “a flexible gravity conveying system with self-tracking skate wheels.” It’s designed for low- to medium-volume, multi-sized conveyance operations, and can be extended, contracted or flexed to meeting material handling requirements, it says.
For future conveyor solutions, Nevenhoven suspects that advancements will include “the reduction in total conveyor footage” in such solutions. He suggests that software-driven picking strategies will eventually not require “miles of accumulation conveyor” that account for imbalances from picking sources or outbound destinations.
“Instead, software will monitor all picking activity, en route case activity and the status of the outbound destinations to perform real-time picking reprioritizations,” Nevenhoven says. “These real-time reprioritizations, or the general change from push-based wave systems to pull-based waveless systems, will be able to mitigate the impact of imbalances, facilitate higher equipment utilization and, ultimately, allow a higher throughput with the use of less equipment.”